The reshoring era: Can the surge survive policy uncertainty?
6 minutes to read
In the aftermath of the COVID-19 pandemic, amid geopolitical flashpoints and a growing desire for national economic resilience, the conversation around reshoring –bringing manufacturing and supply chains back home –has shifted from theory to reality. Once a spectacular political talking point, reshoring became a genuine force reshaping industrial strategies, national policies, and corporate boardroom decisions across the world.
By 2025, major companies across industries were making headlines with billion-dollar announcements: semiconductor giants setting up domestic fabs, automakers reengineering their production footprints, and consumer goods firms scrambling to localise supply chains. This was more than symbolic nationalism; it was a reaction to hard lessons learned from supply chain fragility, geopolitical dependencies, and pandemic-induced shocks.
Yet beneath this apparent momentum, new data and shifting realities suggest the surge may be faltering –not because the logic of reshoring has weakened, but because the terrain has become more treacherous. Legal uncertainties, rising costs, and the need for nuanced, blended strategies are complicating the reshoring picture on both sides of the Atlantic.
The early movers: Headlines and realignment
In the United States, the reshoring wave has been most visible in sectors central to national security and technological competitiveness. Intel invested a staggering $12 billion in two new semi-conductor fabrication plants in Arizona, seeking to reduce dependence on Taiwan and south Korea and bolster America’s position in the chip race. General Motors committed $7 billion to electric vehicle battery production in Michigan, reshoring key components previously sourced from China and Mexico.
Stanley Black & Decker, responding to supply chain turmoil, made headlines by returning its iconic Craftsman tool line from Chinese factories to a gleaming new facility in Fort Worth, Texas. Meanwhile, Tesla and Redwood Materials focused on building a closed-loop EV battery ecosystem inside Nevada, aiming to reduce exposure to vulnerable global supply chains.
Other consumer brands followed suit. Whirlpool increased its investment in assembly plants in Ohio and Tennessee, moving production back from Mexico, while Mars Inc. shifted more of its food and pet care manufacturing from Latin America and Europe into U.S. regional hubs. Across sectors, these decisions were framed as strategic recalibrations designed to bring operations closer to consumers, shorten supply chains, and hedge against geopolitical risk.
Europe’s reshoring push: A quieter but steady rebuild
Across the Atlantic, Europe has embarked on its own reshoring journey, often with less fanfare but no less determination. Driven by the European Union’s industrial strategy and the bloc’s concerns over digital sovereignty, European companies and governments have focused heavily on critical sectors such as semi-conductors and advanced manufacturing.
Taiwan’s TSMC has announced a significant new chip design centre in Munich, Germany, aligned with the EU’s ambition to double its share of global chip production by 2030. Philips, the Dutch electronics giant, has reshored some of its manufacturing from Asia back to the Netherlands, improving lead times and enabling faster responses to European customer needs.
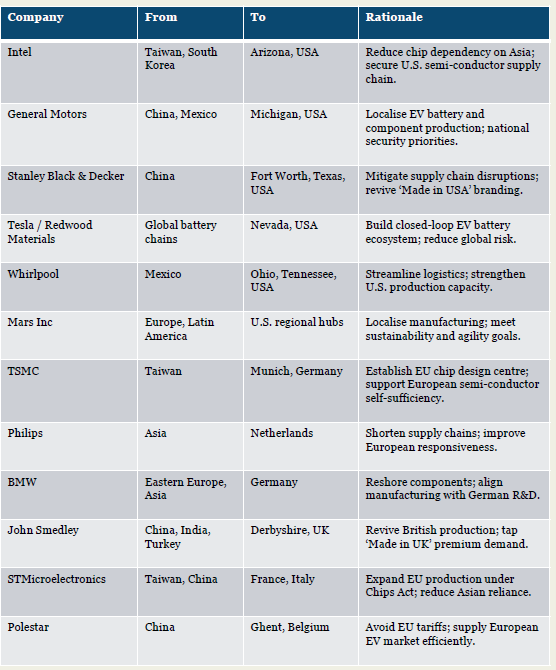
The tariff trap: Legal challenges and uncertainty
Tariffs were originally seen as a sharp-edged tool to drive reshoring, but in 2025, they have become a source of volatility. The U.S. ‘Liberation Day’ tariffs, introduced in April, imposed a 10% baseline duty on most imports, a staggering 125% on Chinese goods, and eliminated the de minimis threshold for small shipments from China and Hong Kong—all designed to shock supply chains into localising.
Yet legal pushback arrived swiftly. In May, the U.S. Court of International Trade ruled that President Trump’s sweeping tariffs, imposed under the International Economic Powers Act, exceeded constitutional authority, stating that regulating international commerce is fundamentally Congress’s job. For a moment, major portions of the tariff regime were struck down – until a federal appeals court temporarily stayed the ruling, leaving the tariffs in place while the appeal process unfolds.
This legal uncertainty has created real-world hesitation. As one trade executive put it to Barron’s, ‘It’s hard to build a five-year investment plan when your cost assumptions can flip with the next court decision.’ What was meant to be a clear incentive for reshoring has, ironically, become a destabilising force.
Is nearshoring just about tariffs?
While tariffs have undeniably catalysed some shifts, the rise of nearshoring – relocating operations to politically aligned, geographically closer countries – is not solely a tariff-driven phenomenon.
The COVID-19 pandemic exposed how brittle long-distance supply chains can be, making resilience a top priority. Firms have realised that having suppliers thousands of miles away, subject to port closures, shipping delays, or geopolitical frictions, carries enormous risk. By contrast, nearshoring offers the ability to respond more nimbly to market changes, reduce lead times, and manage inventory more efficiently.
Trade agreements such as the United States-Mexico-Canada Agreement (USMCA) have made nearshoring to Mexico more attractive by offering smoother regulatory processes and tariff advantages. Countries like Vietnam, Malaysia, and India offer skilled workforces, improving infrastructure, and competitive costs, making them ideal for firms looking to balance risk, cost, and political alignment.
Additionally, sustainability pressures are reshaping sourcing strategies. Shorter supply chains translate into lower carbon footprints, aligning with corporate ESG commitments and consumer expectations for greener products.
In short, while tariffs are an accelerant, nearshoring reflects a deeper, structural recalibration of how companies think about supply chain resilience, efficiency, and sustainability in a volatile world.
The strategic shift: Blending domestic and regional solutions
Recognising these realities, companies no longer pursue reshoring as a pure ‘homecoming’. Instead, they are developing blended strategies that combine reshoring, nearshoring, and friendshoring, underpinned by automation and technology.
Semiconductor firms are expanding assembly in Vietnam and Malaysia; textile producers are moving from China to Mexico and Central America; pharmaceutical companies are building capacity in India and Ireland. These moves don’t abandon globalisation, they reshape it – moving from a flat global model to one built around regional hubs, trusted partners, and multi-local manufacturing networks.
At the same time, automation and advanced manufacturing tools are being redeployed to make domestic production financially viable in high-cost economies. Robotics, AI-driven supply chain management, and smart factory systems are critical enablers of this shift, though they require steep capital investments and bring their own workforce challenges.
Where next? The future of reshoring
The reshoring surge of the early 2020s is not ending, but it is evolving. To sustain momentum, businesses and governments will need to answer hard questions. Can policymakers deliver long-term clarity on trade rules and tariffs, providing businesses with the confidence to invest? Can domestic economies build the infrastructure, workforce, and energy systems needed to support reshoring at scale? Will companies align these strategies with sustainability and ESG goals?
Most importantly, can companies embrace the technological transformation required to offset cost disadvantages and future-proof their operations?
The reshoring era is not about going backward to old industrial models; it’s about reimaging production in a world where geopolitical, economic and environmental pressures intersect. Firms that get this balance right will not only survive the turbulence – they will emerge stronger. The reshoring era is here, but whether it thrives or falters will depend on how well leaders – in business and government – navigate the stormy waters ahead.